Part 2: The Printer
In my last PRS post I broached the idea of having an onboard 3D Printer to fabricate parts. After much consideration I decided to go with an economical, mid-range printer for the test. I needed one capable enough to make a variety of parts, with a good size build volume to handle more ambitious prints. It also had to be able to use a variety of filaments including PLA, ABS, PETG, Nylon and Carbon Fiber Polycarbonate. The other factor was cost, primarily because I wasn’t sure if there would be some unforeseen issue with it living aboard Sérénité with me, thus I didn’t want to spend a lot only to have it get trashed. My printer of choice was the AnyCubic Vyper.
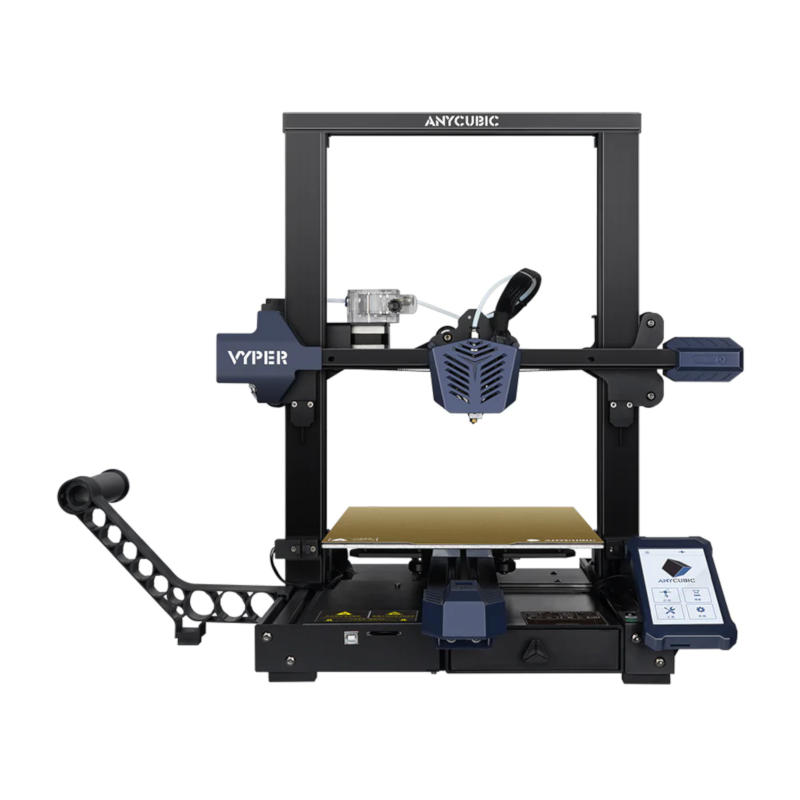
For an inexpensive printer I have been really pleased so far. I had some initial problems with the fans on the print head and with the heated bed, but AnyCubic customer support was great and they sent me the replacement parts quickly – and under warranty. I’ve had it for over a year now and it’s still going strong. When I first purchased it I had quite the backlog of printing for it to do. It was more-or-less in continuous operation for a couple of months 😉 after that I upgraded the hot end and switched to using steel nozzles – the brass ones wear out pretty fast when you are printing with the more abrasive filaments.
Examples
There are a lot more examples than the ones shown below and I’ll be posting them later in the blog post about project to which they belong.
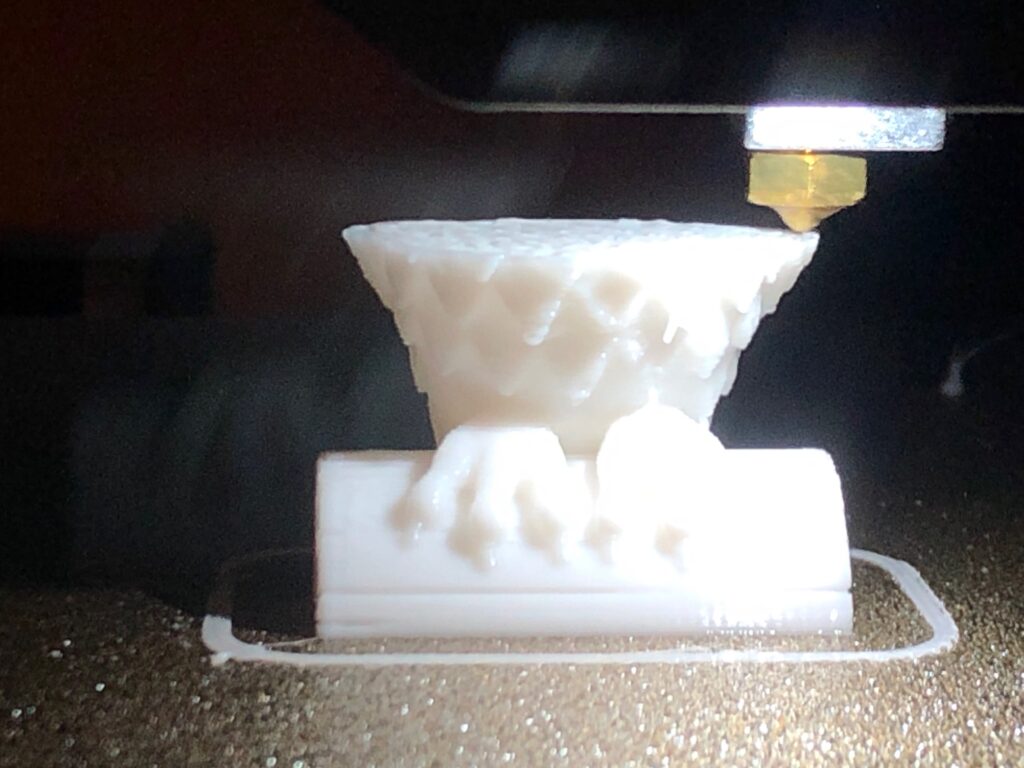
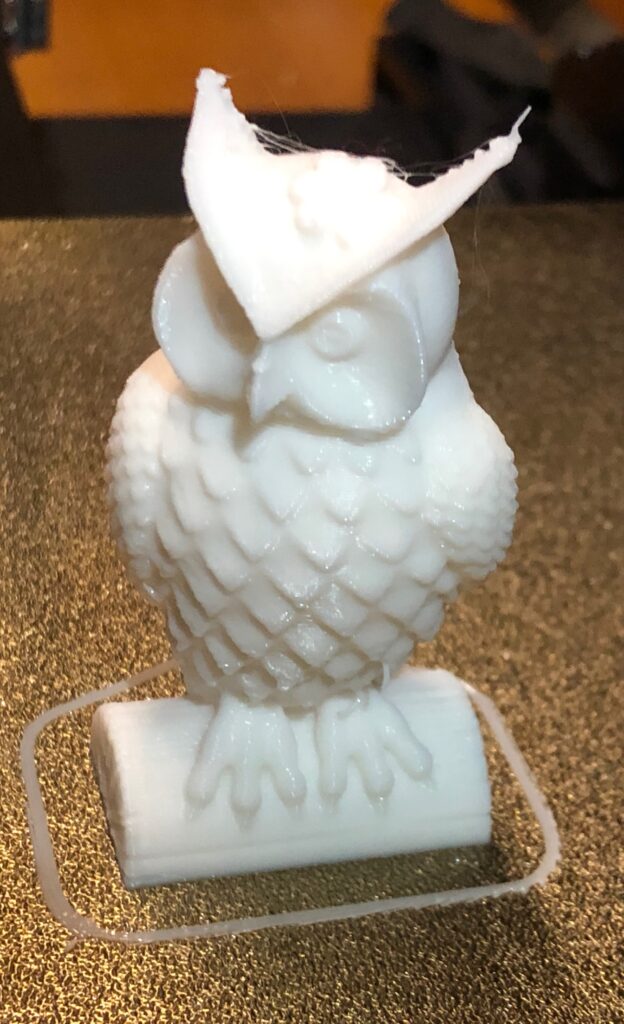
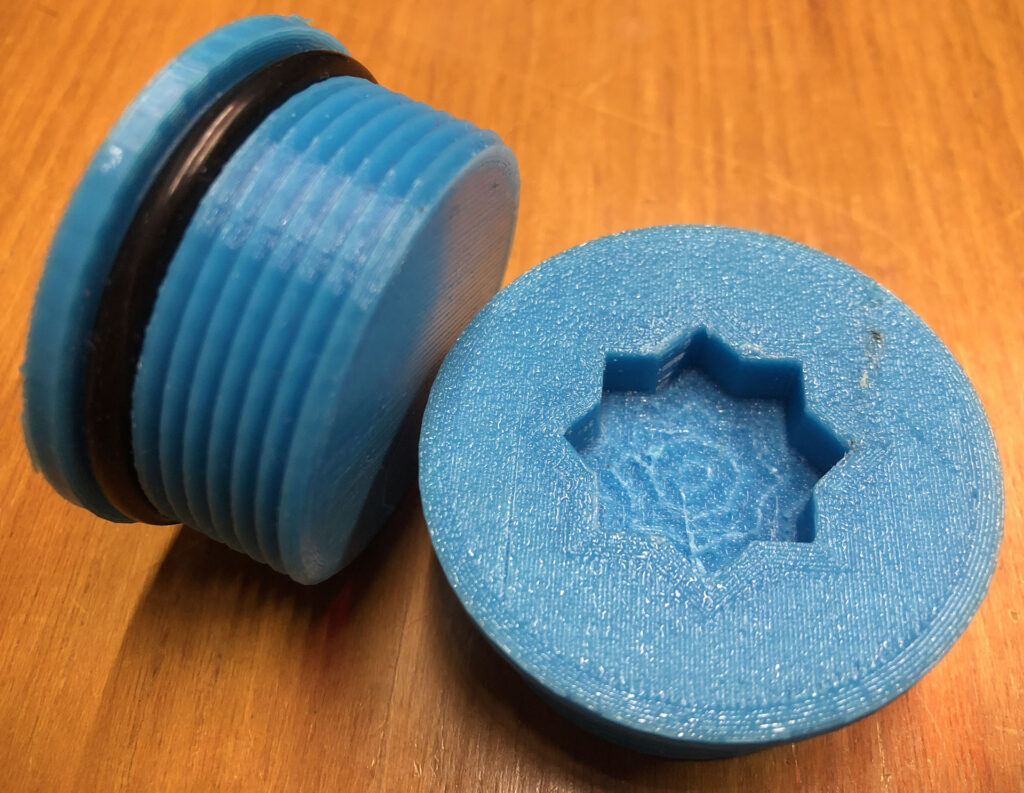
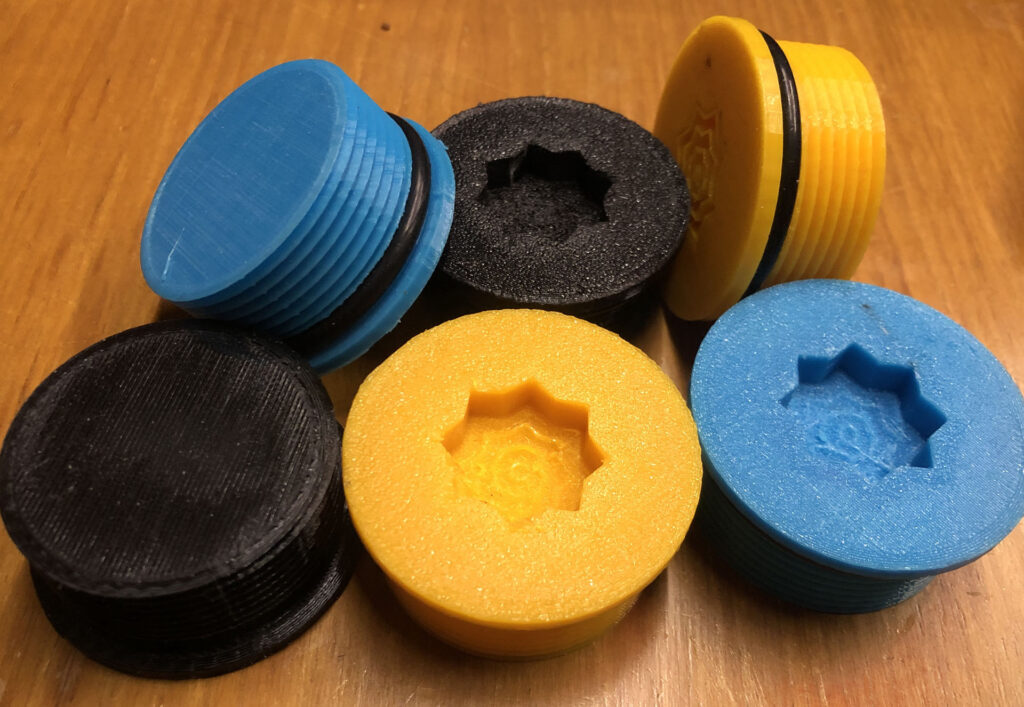
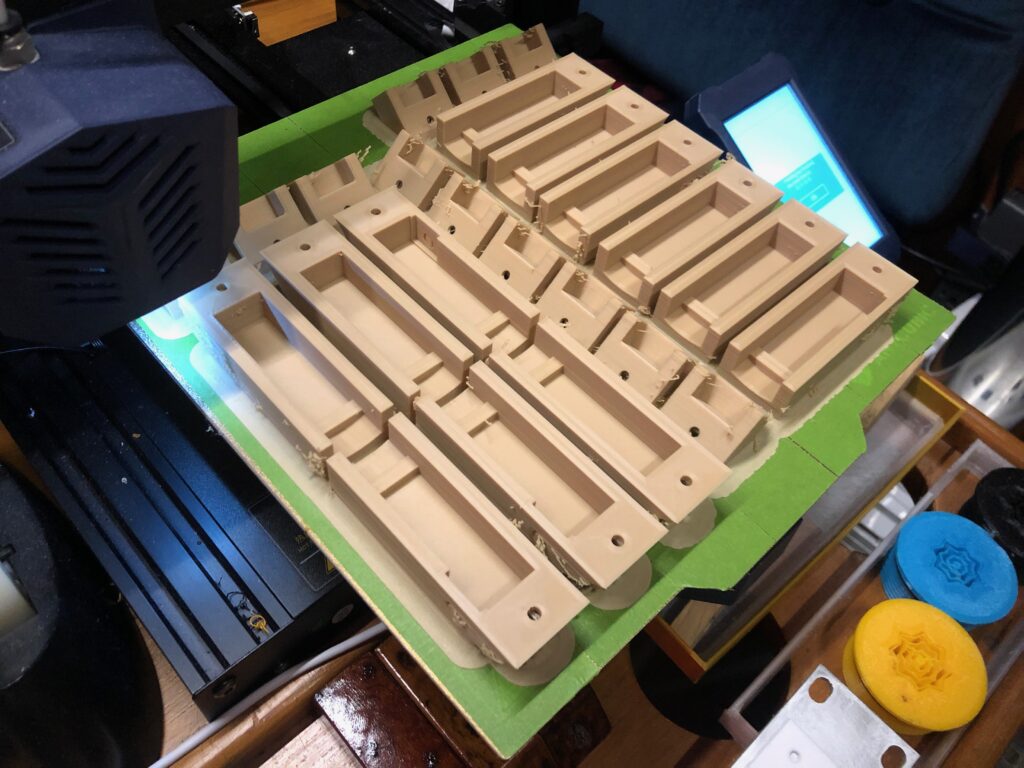
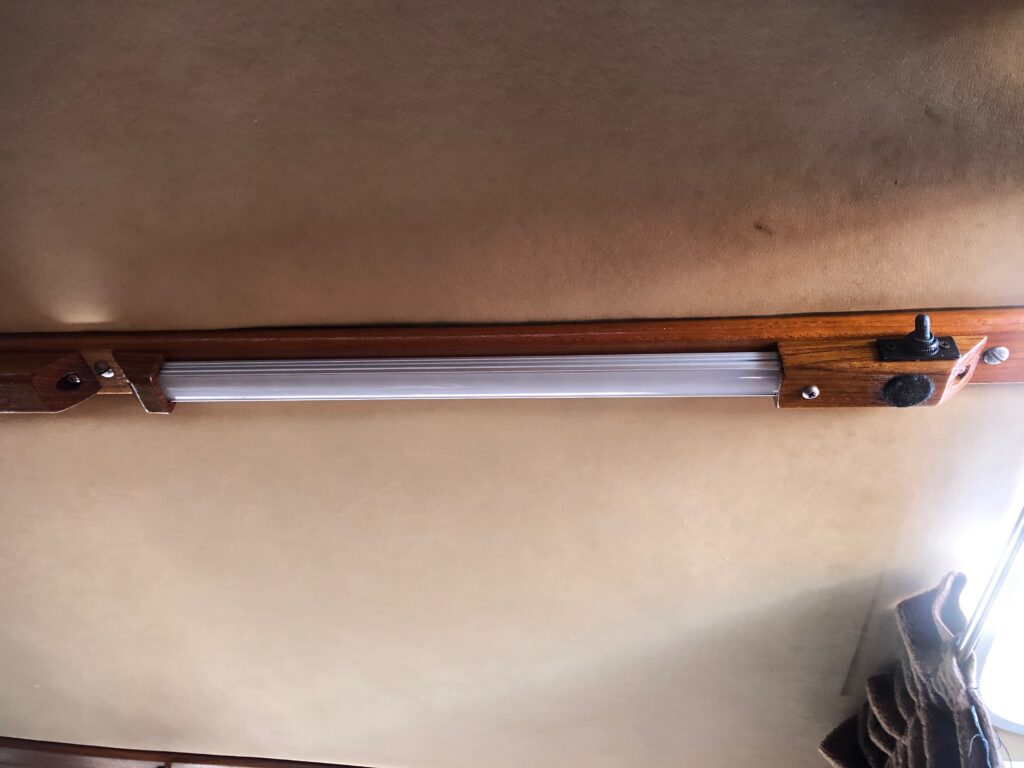
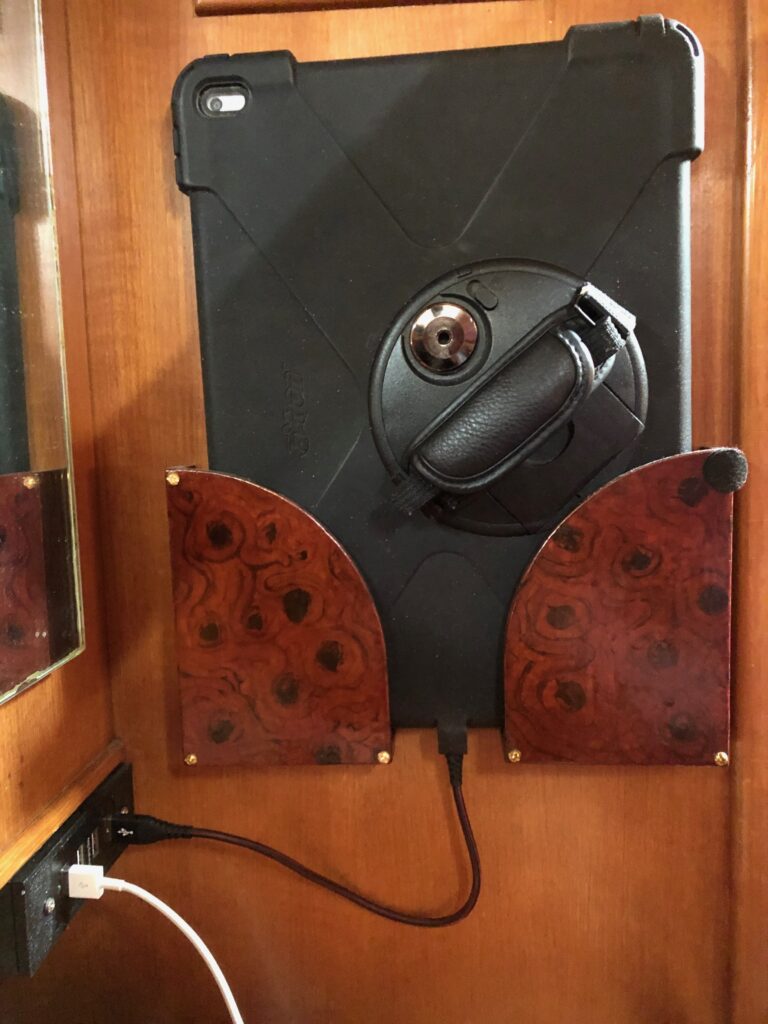
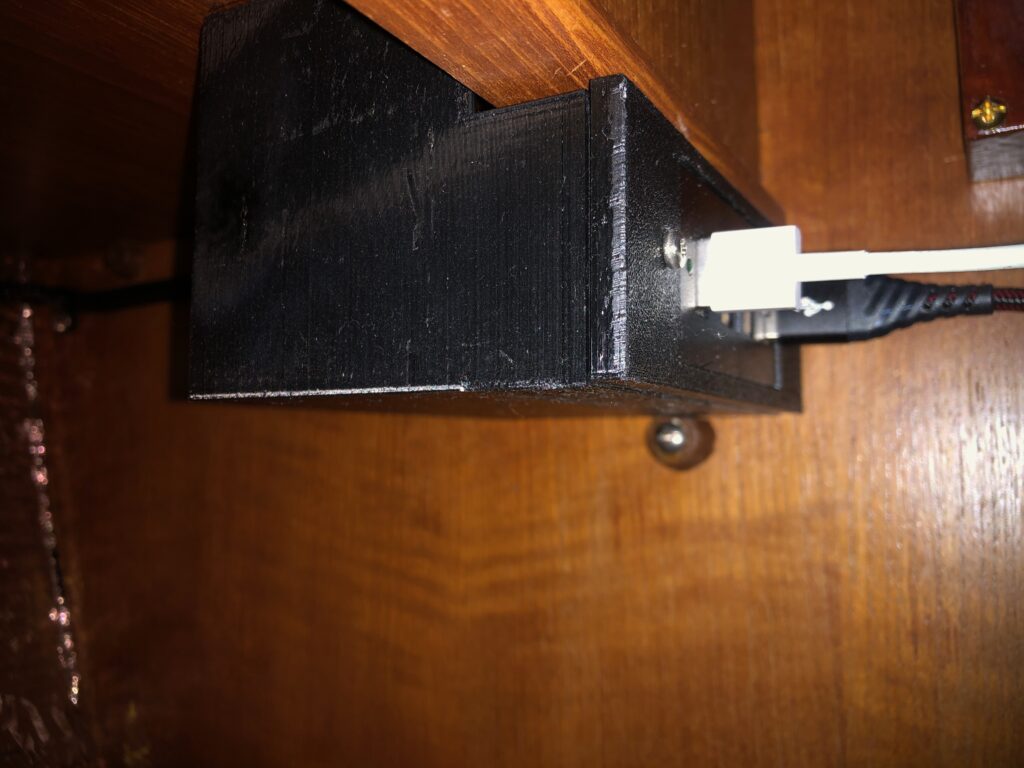
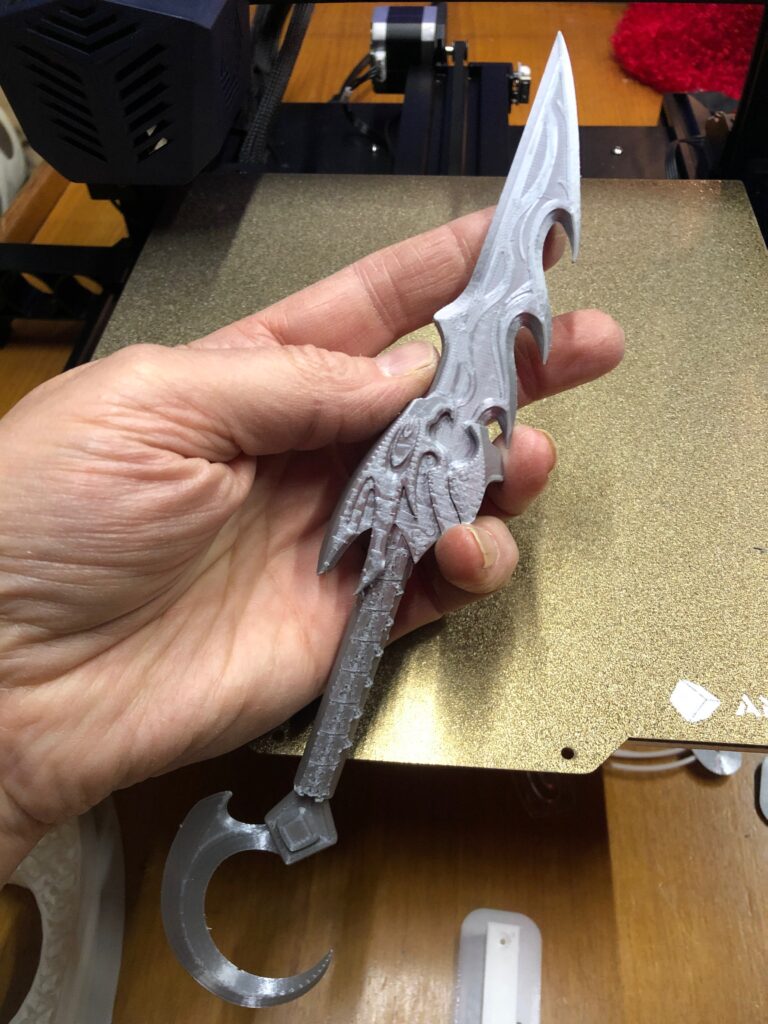