Adding a sturdy sailing arch to Sérénité will provide space to attach the radar dome, antennas, and davits for the dinghy. It will also be the lynchpin in the larger project of “greening” power generation aboard Sérénité. The arch will serve as the attachment point for two wind generators (port and starboard) and form the rear support of the frame for mounting several large solar panels. The panels will also form a hard top over the cockpit, providing shade and protection from the weather. Later, to the frame, arch, and solar panels, canvas sides will be attached to form a fully enclosed cockpit.
Step one is to remove all the hardware from the rear of the boat, railings, cleats, existing radar/wind generator pole – it all has to go! Fortunately the steering pedestal is already out as part of the separate cockpit refurbish project, which is on hold till the arch is on.
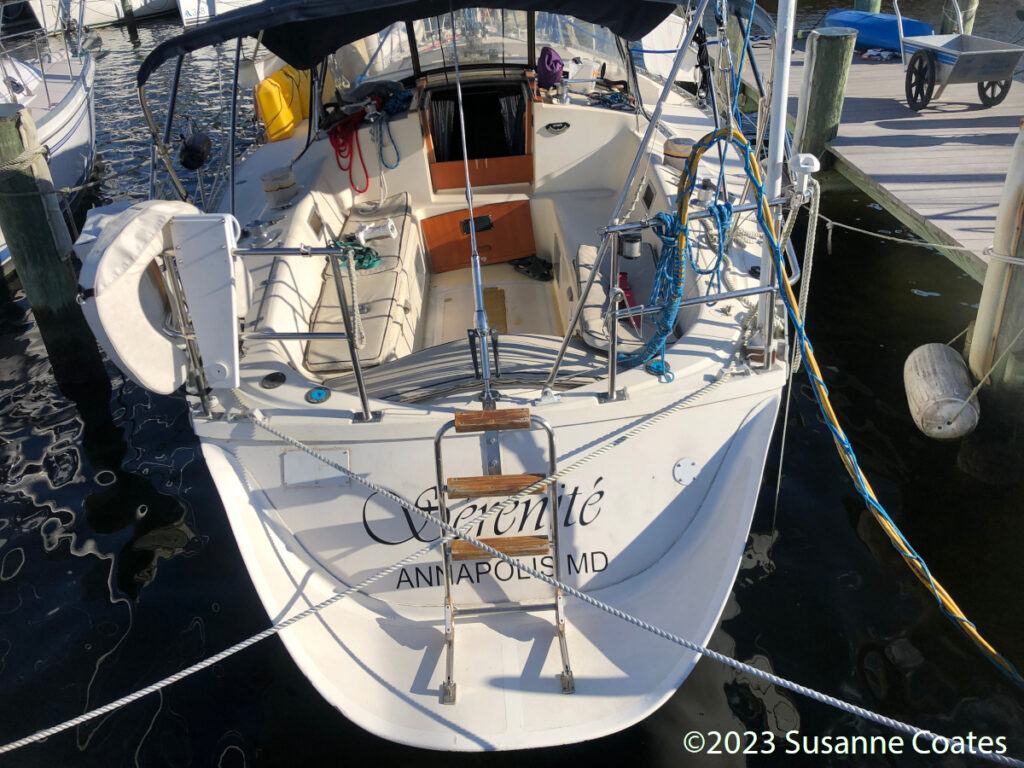
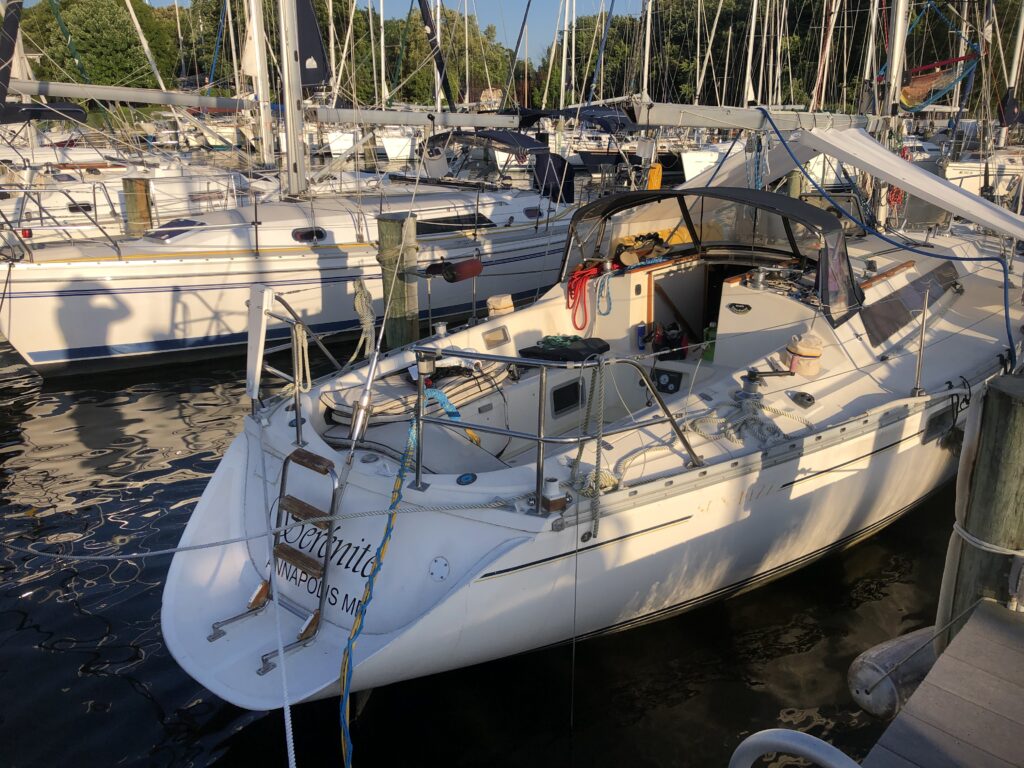
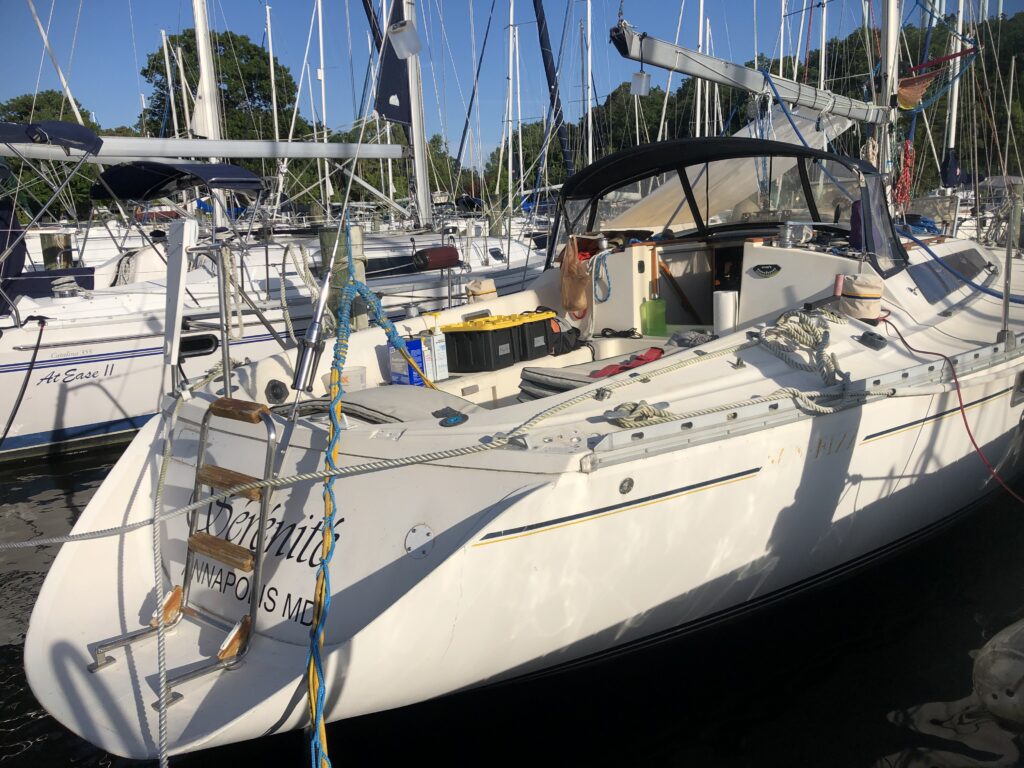
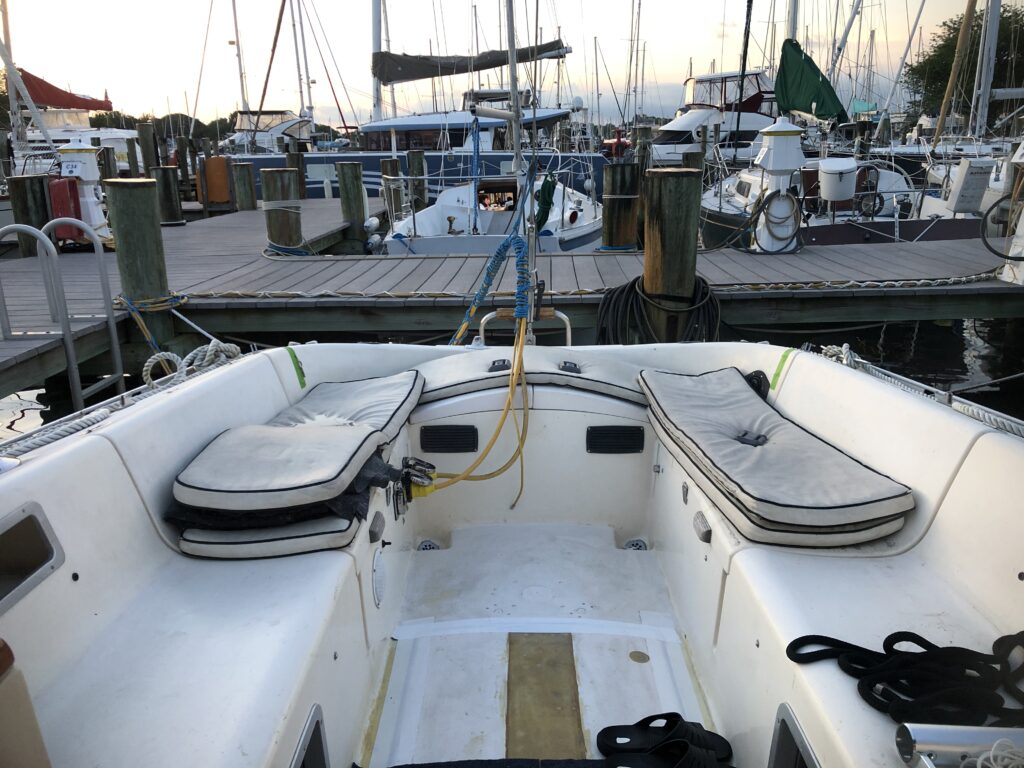
Fitting the arch to the boat is a tedious process that involves repeated trimming, standing the arch up on the back of the boat, measuring, then trimming a little more – trim, measure, repeat!
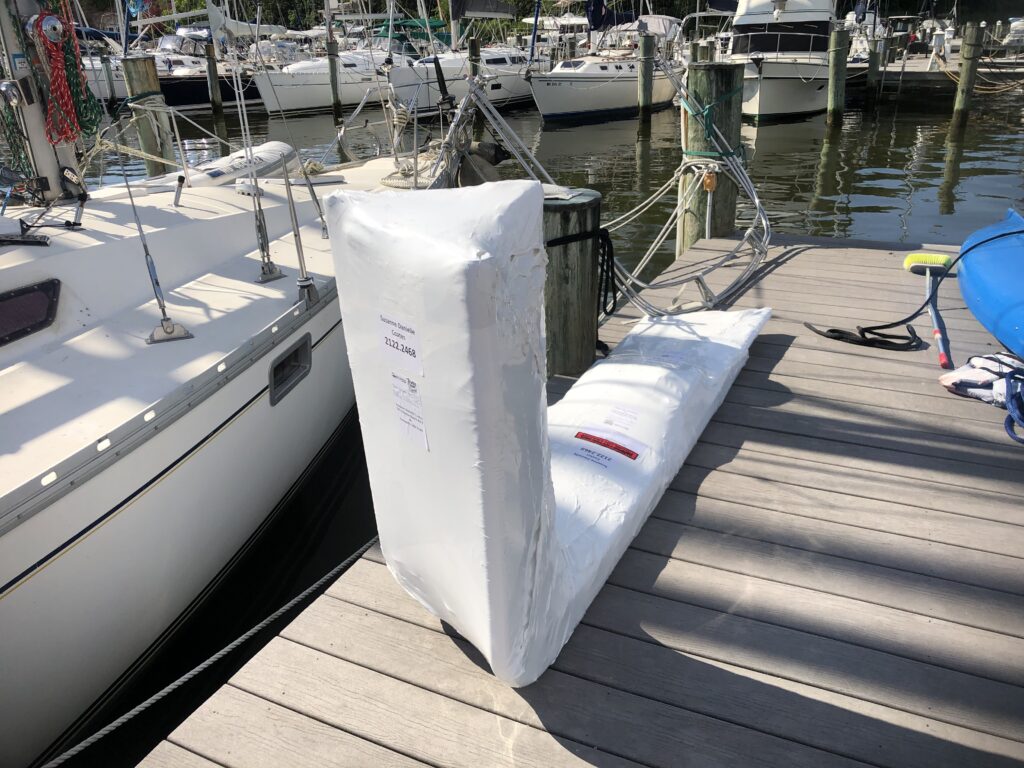
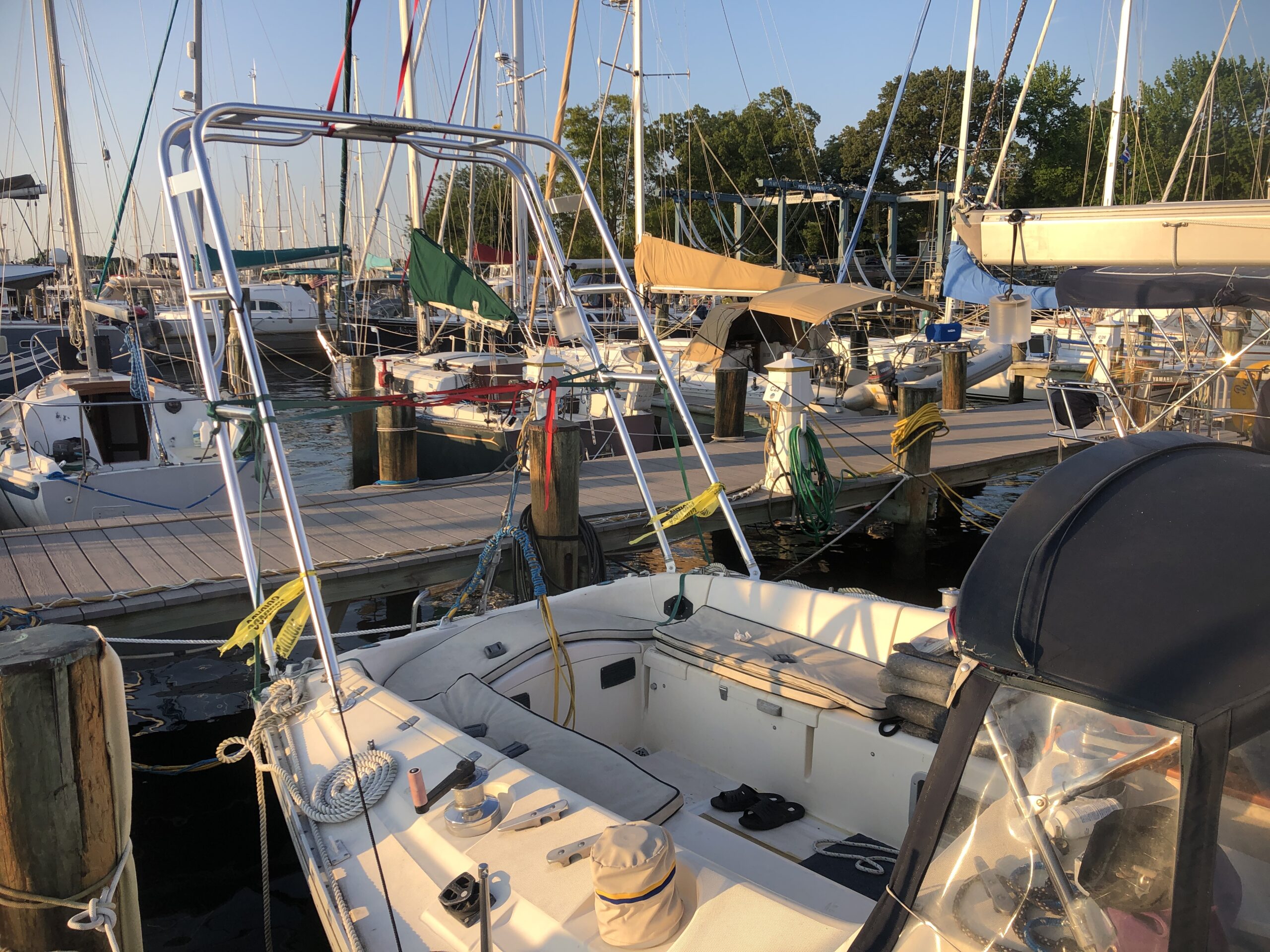
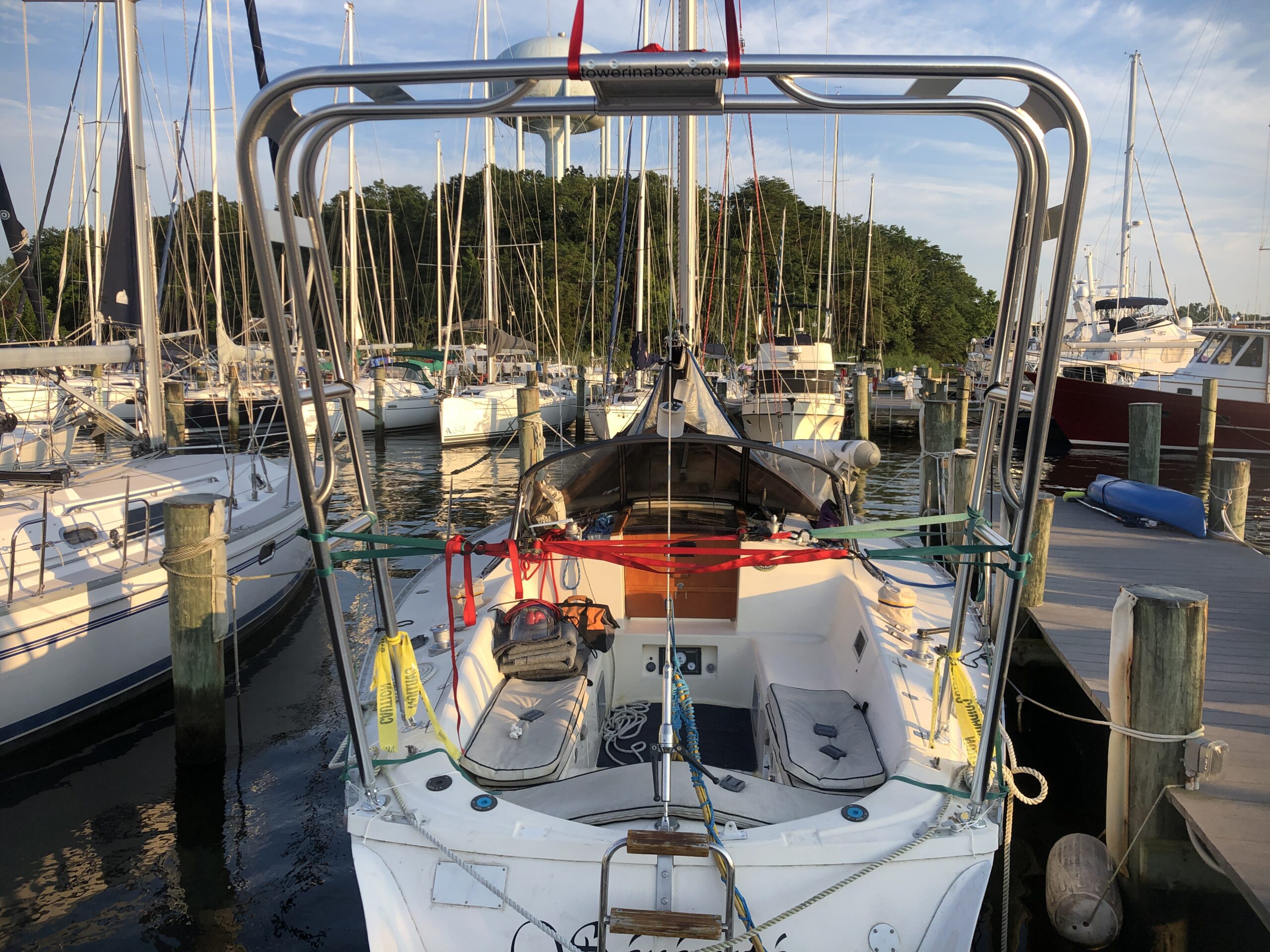
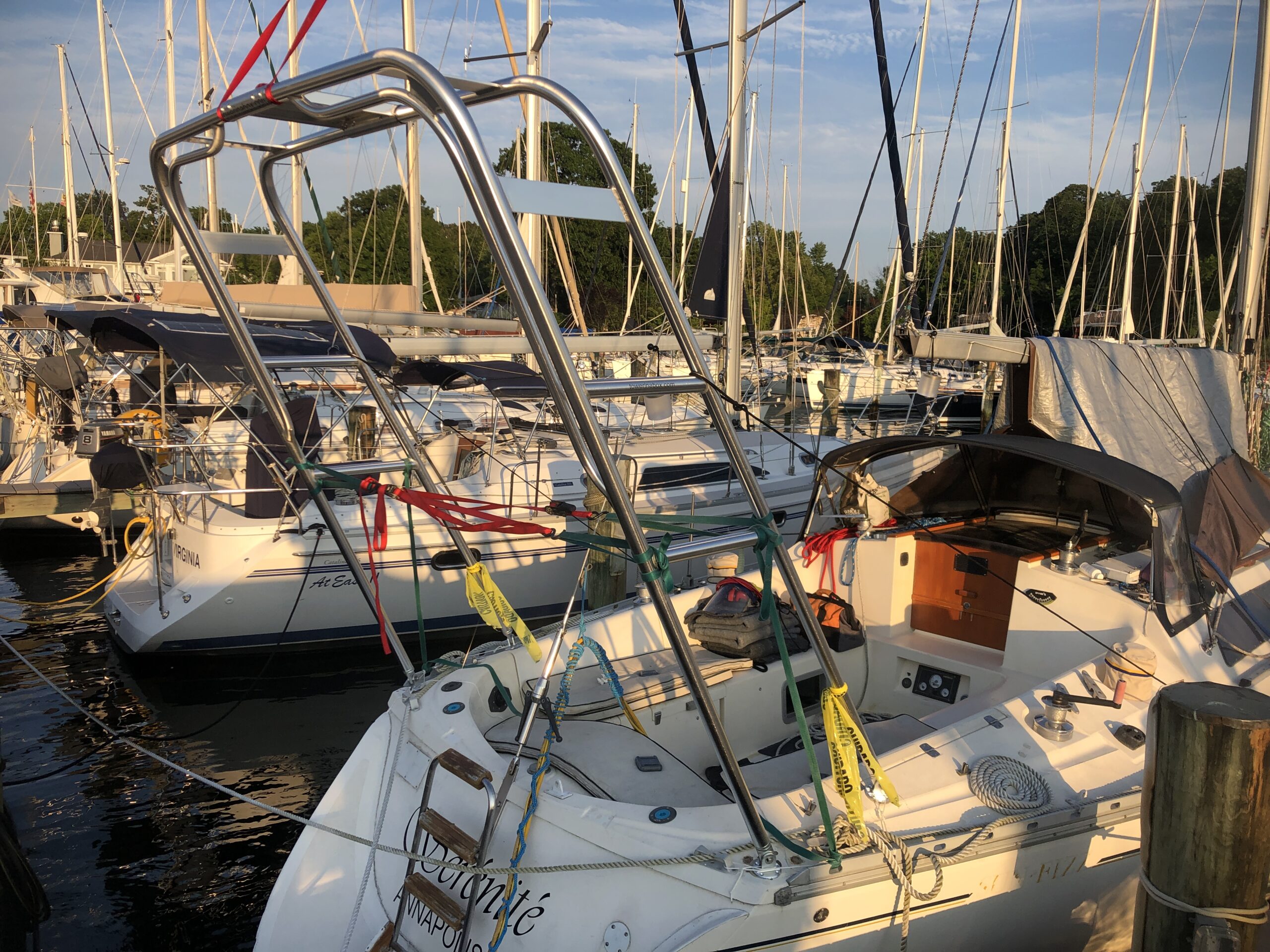
Since I will have the deck reinforced by professionals I will only trim enough to get an idea of the approximate locations where the feet will land on the deck. After the reinforcing is complete I will complete the fitting process.




The Port Annapolis crew did a great job on the deck reinforcement (Kudos to Rick and Taylor). Photos below are of the port side work, the work on the starboard is mirror-identical.

Then, my part – the (hopefully) last round of cutting and fitting of the arch – went well with one minor exception: The spot where the back legs land on each side (port and starboard) is slightly curved owing the the sculpting needed to get the new reinforcement to blend with the existing deck hardware.
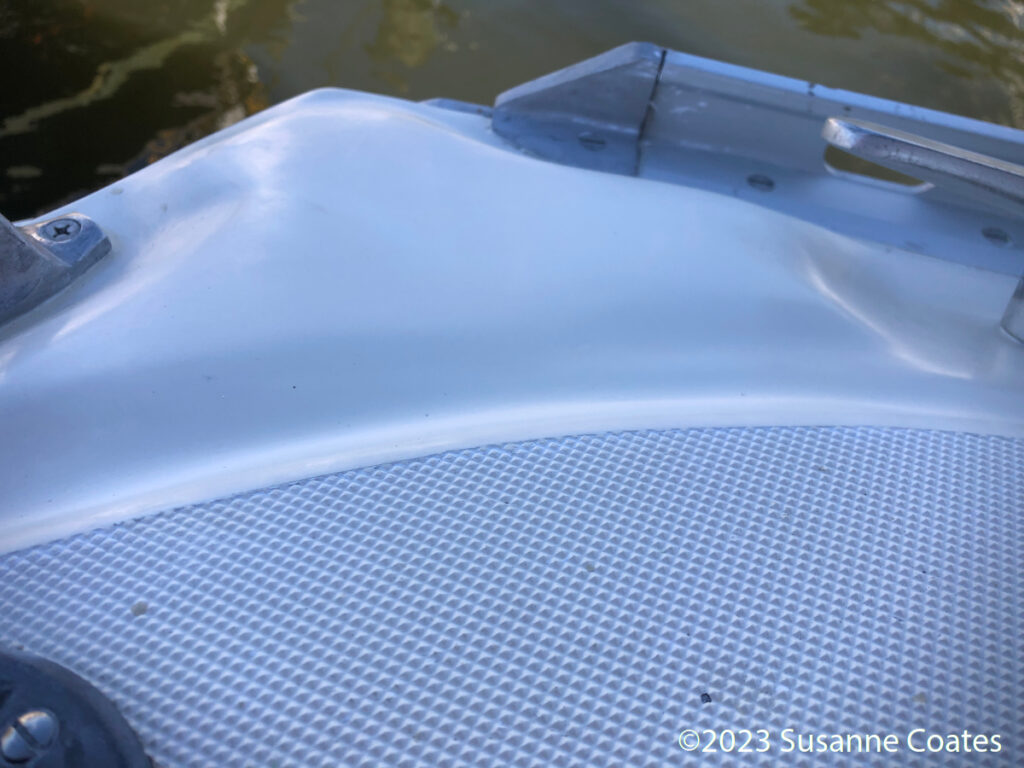
So, one more thing is needed to ensure that the arch base plates for the rear legs are not overstressed when mounted in position on a slightly curved surface. After consulting with Port Annapolis’s repair and improvement guru – Rich Krolak – the optimal solution was determined – aluminum reinforcing plates. The plates shown below were purchased from McMaster-Carr and are fabricated from high-strength aluminium, 90mm diameter rod stock cut to 8mm thick. I drilled the holes on the drill press in my shop. The presses laser guides were key for getting the holes in the reinforcing plates aligned with those in the base plates. And, a bit of advice if you’ve never drilled in to high strength aluminum, be sure to use plenty of cutting lubricant!
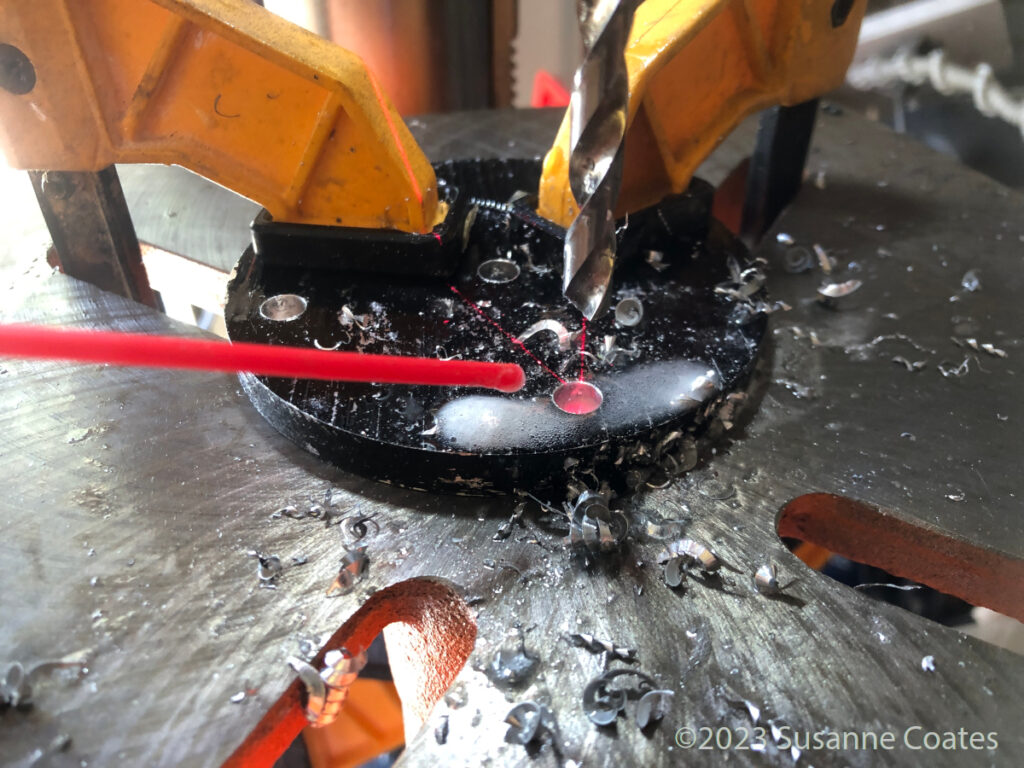

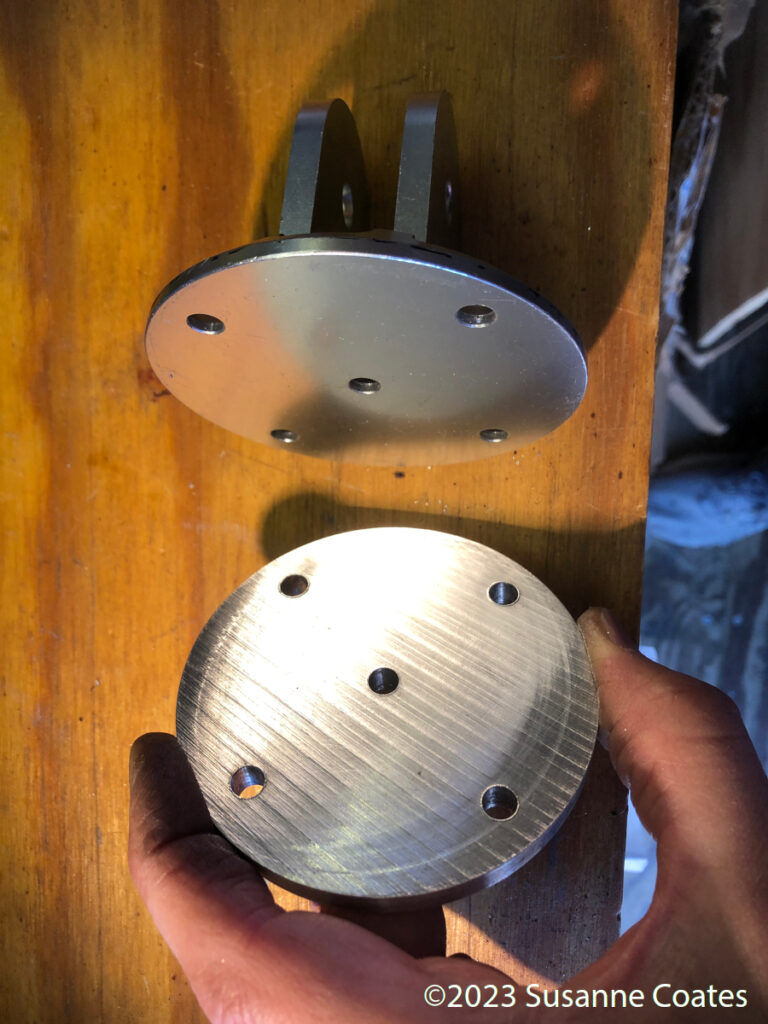
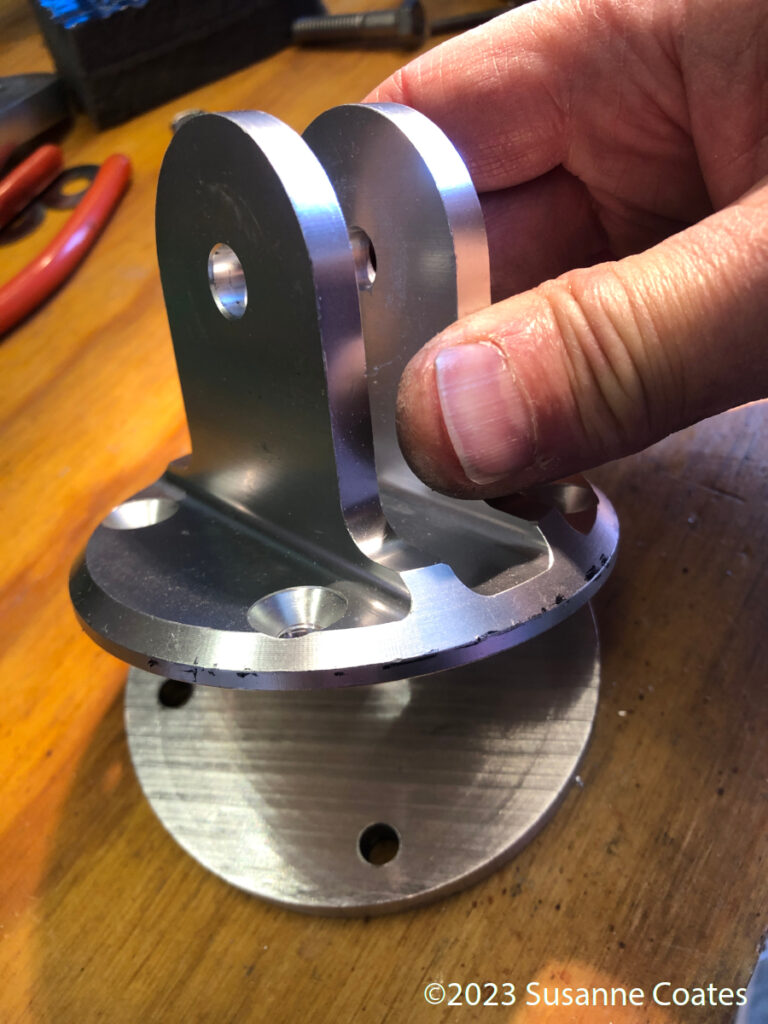
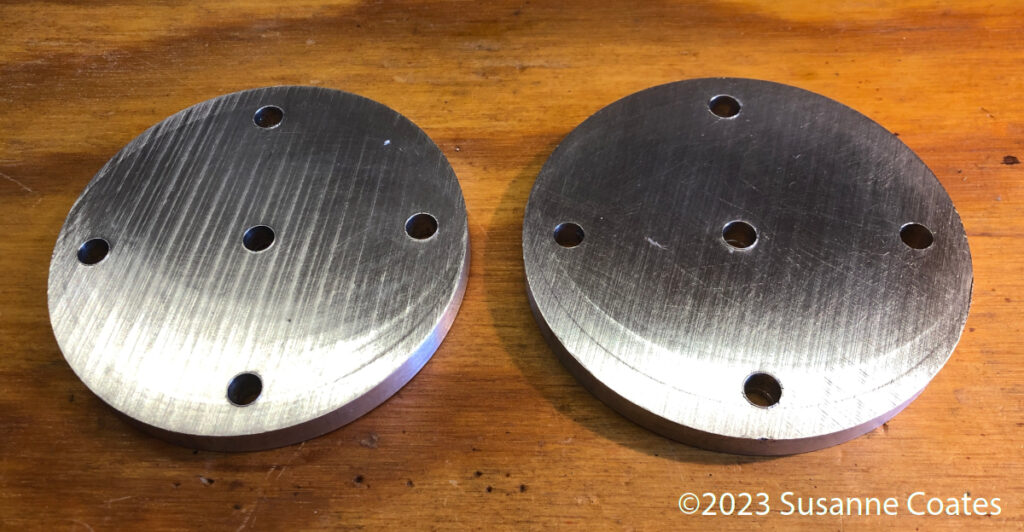
So, at this point with all the prep work done, last remaining task is to mount the arch! That will be the subject of the next post!